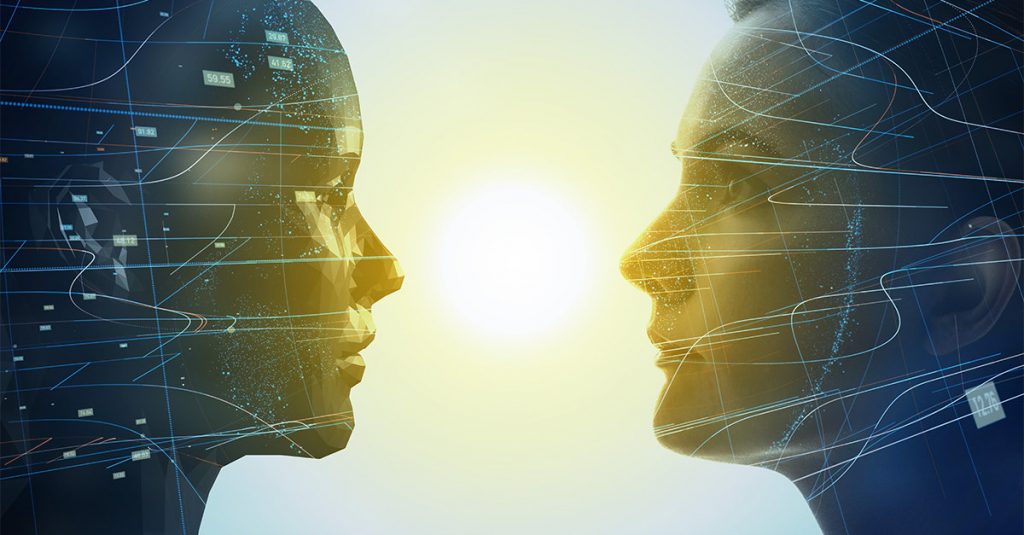
As warehouse operations grow in complexity, many organizations turn to digital twins to increase their performance capabilities. Digital twins are virtual replicas of physical entities and their interactions with one another. The technologies in a digital twin capture real-time data to support improvements and decision making. This project focuses on digital twins as a promising solution for enhancing performance metrics within a warehouse operation, including efficiency, productivity, and scalability, particularly in the picking process. Because order picking is one of the most labor-intensive activities in the warehouse, we examined the feasibility of employing machine learning to forecast labor requirements. To develop a digital twin prototype for the order-picking process, we explored several technologies aimed at improving efficiency and productivity: sensors, automated guided vehicles (AGVs), picking robots, and automated storage and retrieval systems (AS/RS). By conducting stakeholder interviews, process mapping, and gathering data pertaining to historical order demand and daily labor hours, we formulated a workforce forecasting model that harnesses machine learning techniques. Leveraging the forecasting model alongside the recommended technologies will allow the warehouse team to enhance their key performance indicators (KPIs) for efficiency and productivity. This project culminates in a comprehensive roadmap for implementing these solutions, with the potential for scaling this digital twin prototype to other processes and warehouses. Read more.